Dual-mode design to meet diverse work scenarios
Learn more about how this uniquely designed versatile wrench combines the benefits of a traditional open-end wrench with a dual-purpose wrench. Through a simple switching mechanism, users can freely change the tool form on different types of bolts and screws, which greatly improves work efficiency. Whether it is fine adjustment in a small space or the fastening of large parts, this wrench can be competent and free, become the ideal assistant for all kinds of maintenance tasks.
Imagine replacing spark plugs in a crowded engine compartment. The traditional single-function wrench may leave you helpless, but with this new multi-function wrench it is completely different. It can not only be used as a regular open-end wrench, but also can be quickly converted into a ratchet wrench for continuous rotation operation. This flexibility not only saves a lot of time and effort, but also reduces the chance of mistakes caused by frequent tool changes. Not only that, the product is also equipped with precise scale identification and non-slip tooth design, so that users can obtain a stable and reliable grip at any angle.
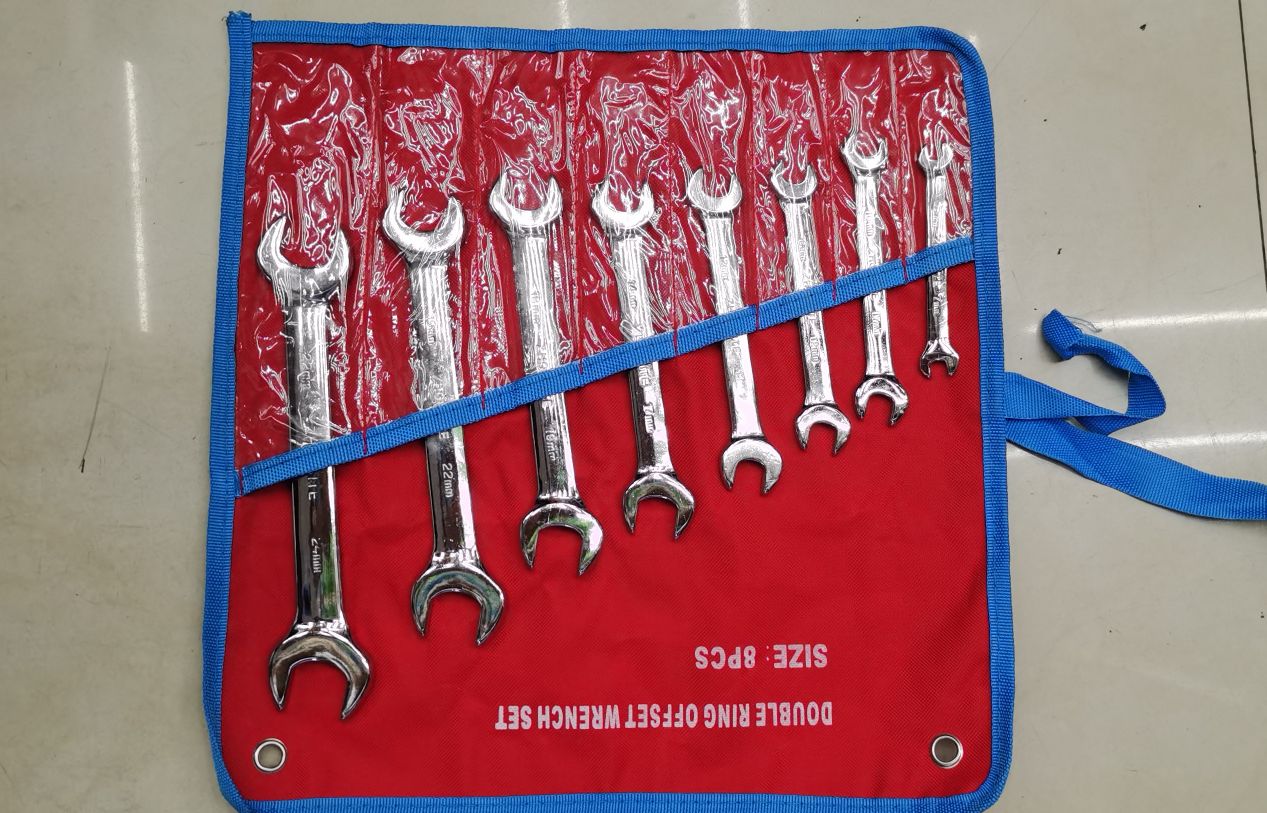
Suitable for a wide range of applications, from home DIY to professional fields
Discuss the practical application scenarios of this wrench in household maintenance and personal projects. For home users who love hands-on, it is an indispensable good helper, which can easily handle various trivial matters such as daily home repairs and bicycle maintenance. For professionals, it is an important tool for them to deal with complex machinery and equipment on the construction site or in the workshop. Whether it's a car mechanic, a master carpenter or an electrician, you'll find that the convenience and efficiency of this tool far exceeds expectations.
Take an ordinary father as an example. On the weekend, he plans to replace the old chair at home with a new armrest. In the past, it may be necessary to purchase many different pieces of manual equipment to complete this seemingly simple but time-consuming task; now it is enough to have such a multifunctional wrench. It can be used to unscrew the small screws that fix the foot of the chair, it can also be used to remove the aging hinge pin, and it can even assist in cutting metal plates and other extraordinary functions. Similarly, technicians working in industrial environments are also full of praise. Because this wrench is not only adaptable, but also has extremely high durability, it can maintain a long-term good condition in a harsh working environment.
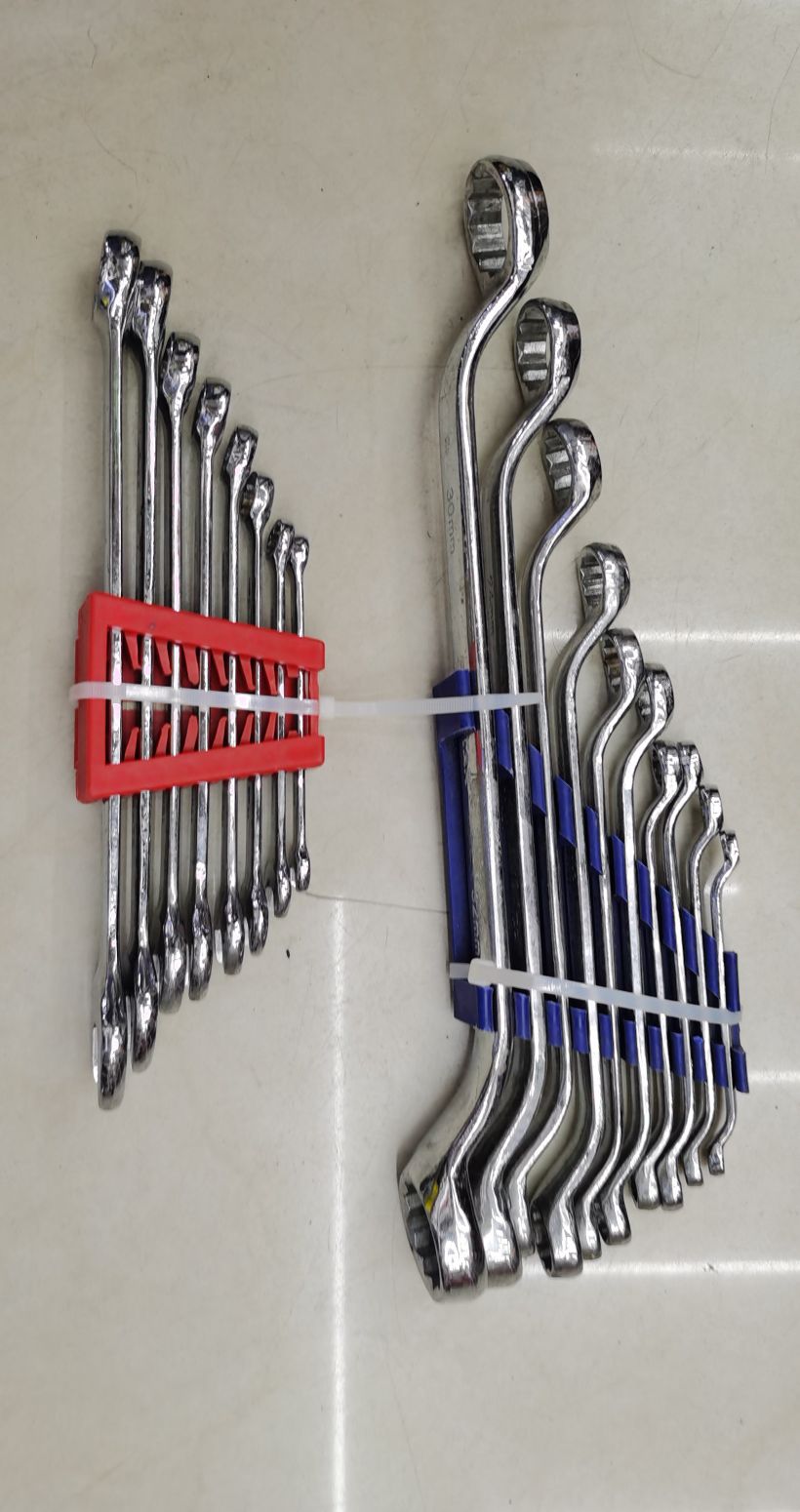
Rugged, durable and reliable quality assurance
Explain in detail why this multifunctional wrench has excellent service life and stability. It is made of high-strength alloy material and polished by precision machining process, which makes the overall structure extremely strong and not easy to deform. The surface has also been anti-corrosion treatment, even if long-term exposure to wet environment can maintain smooth as new. Coupled with humanized design concepts, such as comfortable grip shape and anti-slip texture, further enhance the user experience. All this ensures that this wrench can operate stably under harsh conditions for many years without losing precision.
In order to achieve the above excellent performance indicators, the manufacturer has adopted the most advanced production equipment and technical processes. The first is to strictly screen the raw materials and select only those high-grade steel with the best quality and in line with industry standards. The next step is to send these selected raw materials into the automated production line to undergo multiple forging and extrusion processes, thus forming a dense and tough overall framework foundation. The last step is to implement a special chemical coating spraying operation on the appearance part, giving it a variety of protective properties such as anti-corrosion and waterproof, but also greatly extend the life of the product. At the same time, the designers fully considered the principles of ergonomics, and carefully carved an artificial rubber gasket suitable for palm fitting in the handle, which greatly improved the grip comfort.
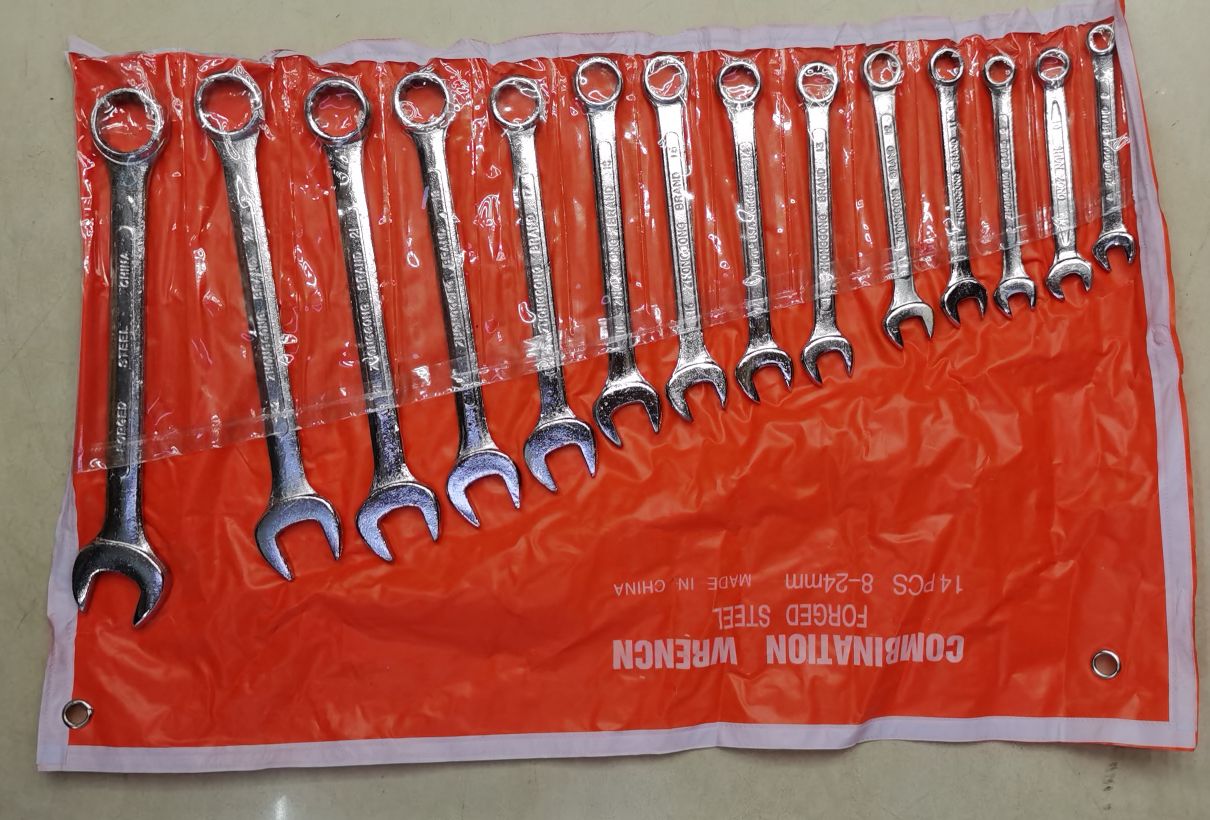
Accurate calibration, every operation is perfect performance
Emphasize the attention to detail in the manufacturing process of this versatile wrench. Each part is produced in strict accordance with high standards, and then assembled and debugged by a team of experienced engineers. Before leaving the factory, we must go through a series of strict inspection procedures, including torque testing, pressure testing and other links, so as to ensure that the finished product has excellent operating performance and smooth feel. What is finally presented to consumers is a professional-level tool that can stand the test, allowing users to enjoy the ultimate control experience every time they pick it up.
From the initial concept to the birth of the final product, the entire research and development cycle lasted more than two and a half years. During the investment of a large number of human and material resources to test and improve the design scheme, and strive to achieve perfection. For example, the use of laser welding technology to replace the traditional riveting method at the key connection nodes not only reduces the number of potential failure points but also significantly improves the connection strength. For the key positions that are easy to wear, a special composite material is specially customized as a wear-resistant layer to effectively prevent the loss caused by long-term friction. In addition, every nut, every spring and even the smallest ball bearing must be screened one by one before being allowed to join the assembly line.
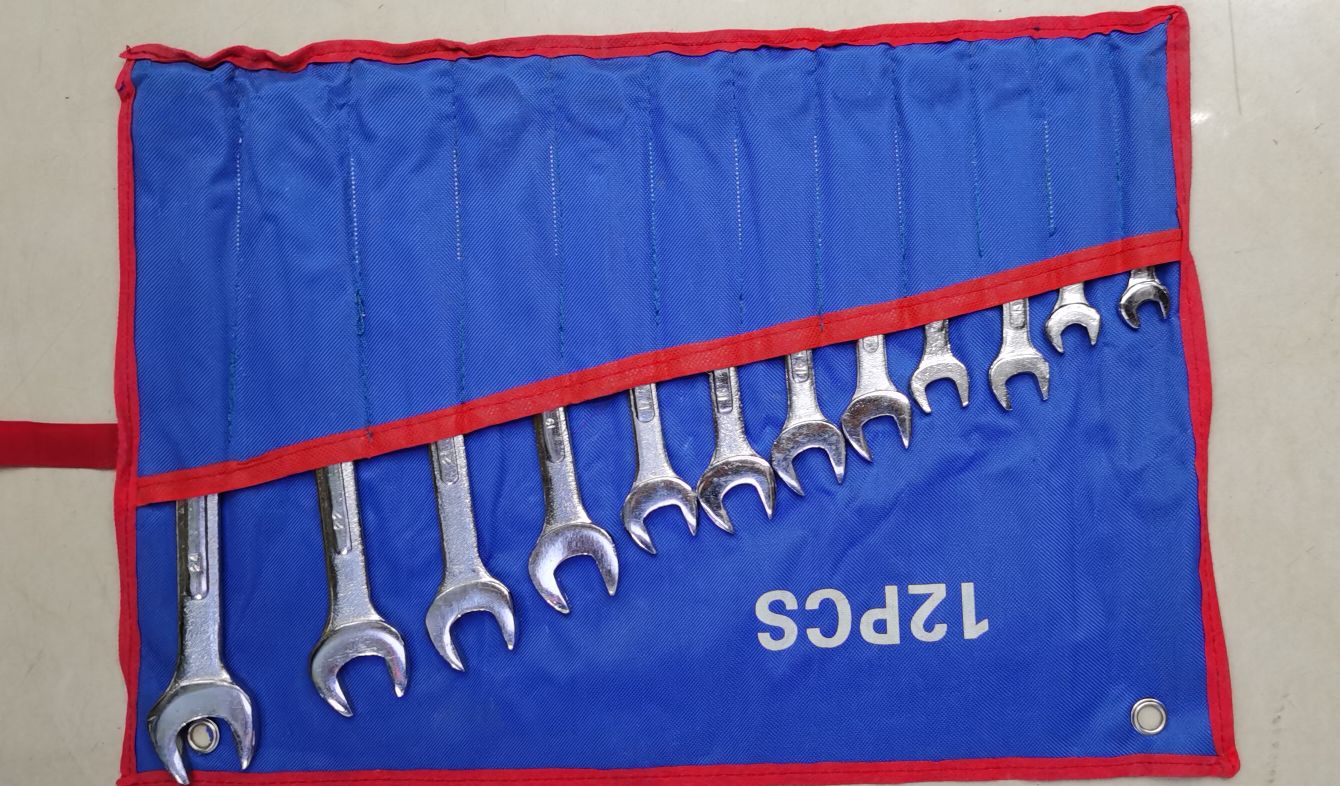